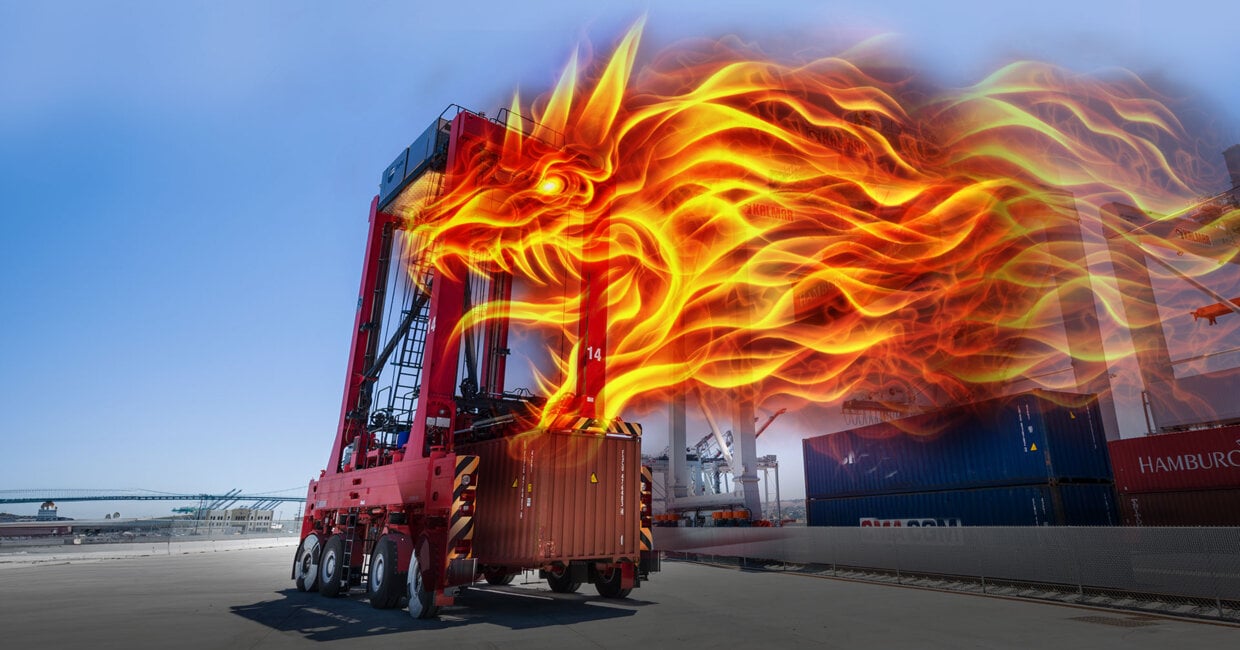
Myth #5: Container scheduling and decking should be done by the TOS
To wrap up this series on the automated straddle carrier concept, we need to put to rest one final untruth. This is the idea that the Terminal Operating System is the best place to handle decision-making for the decking and scheduling of containers at the terminal.
This may have been true for manually operated terminals, back when we didn't have better tools. Today it isn't, and we have.
At manual terminals, there haven't been any other software solutions available, so it's been natural to handle the top-level decking and scheduling decisions in the TOS, and to pass on the implementation to the drivers on the ground. At an automated terminal, this simply doesn't cut it anymore. To get the optimum performance out of automation, we need to use the best tools available, along with all relevant data to provide us with situational awareness on the status of each machine and container. In practice, this means handling some or most of the container scheduling and decking at the level of the automation system and/or the equipment control systems.
Right place, right time
In the simplest possible terms, as the automated straddle carriers are bringing one container from the quay crane to the yard, the system will already know which container will need to be loaded next, so the two can be placed close to each other. If the decking is simply carried out according to predefined rules in the TOS, there is no coordination between these two container moves. The key is to minimise the amount of unproductive moves for the horizontal transportation. Scheduling, decking and routing decisions are interconnected and therefore in an optimised system they should be made together.
Handling the decking at the level of the automation system also introduces other opportunities for optimising traffic in the yard. For example, container operations can be timed to take place at every second container row at any given time, eliminating the need for multiple automated straddle carriers to drive along the same wheel paths in the stack. This kind of optimisation is not possible with manual operation, since the TOS generally doesn’t have the functionality to handle decking in such detail.
Connecting the dots
The benefits of integrating the decking and scheduling with the automation system also extend to landside operations. At an AutoStrad™ terminal, we know the exact position and route of every straddle carrier and container, so it would be easy to suggest the best lane for an incoming road truck that is coming to pick up the container, instead of leaving the matter to chance and having to deliver the container to wherever the truck ends up.
Finally, in addition to optimising the movement of containers at the terminal, another benefit of removing the decking and scheduling from the TOS is that it simplifies system integration considerably. At the TOS level, it's enough to provide the end goal of where the containers are coming and going, and the automation system will handle the rest. However, this is not an either/or choice, and depending on what works best, the automation system can select the exact container slot or just the general area where the container should be placed. The options are there, so we might as well make use of them.
Related articles
Further reading
Subscribe and receive updates in your email
Unsere Veröffentlichungen abonnieren